Optimising your design
After receiving a design, we check the required technical adjustments to enable us to produce the decor using our specific print process. Don’t worry, your design won't be changed – just optimised for the printing process.
One of our qualified gravure cylinder suppliers will use your files to produce the printable data. Before the cartons are printed, you'll receive another PDF file for approval of texts and a color-accurate proof to approve colors.
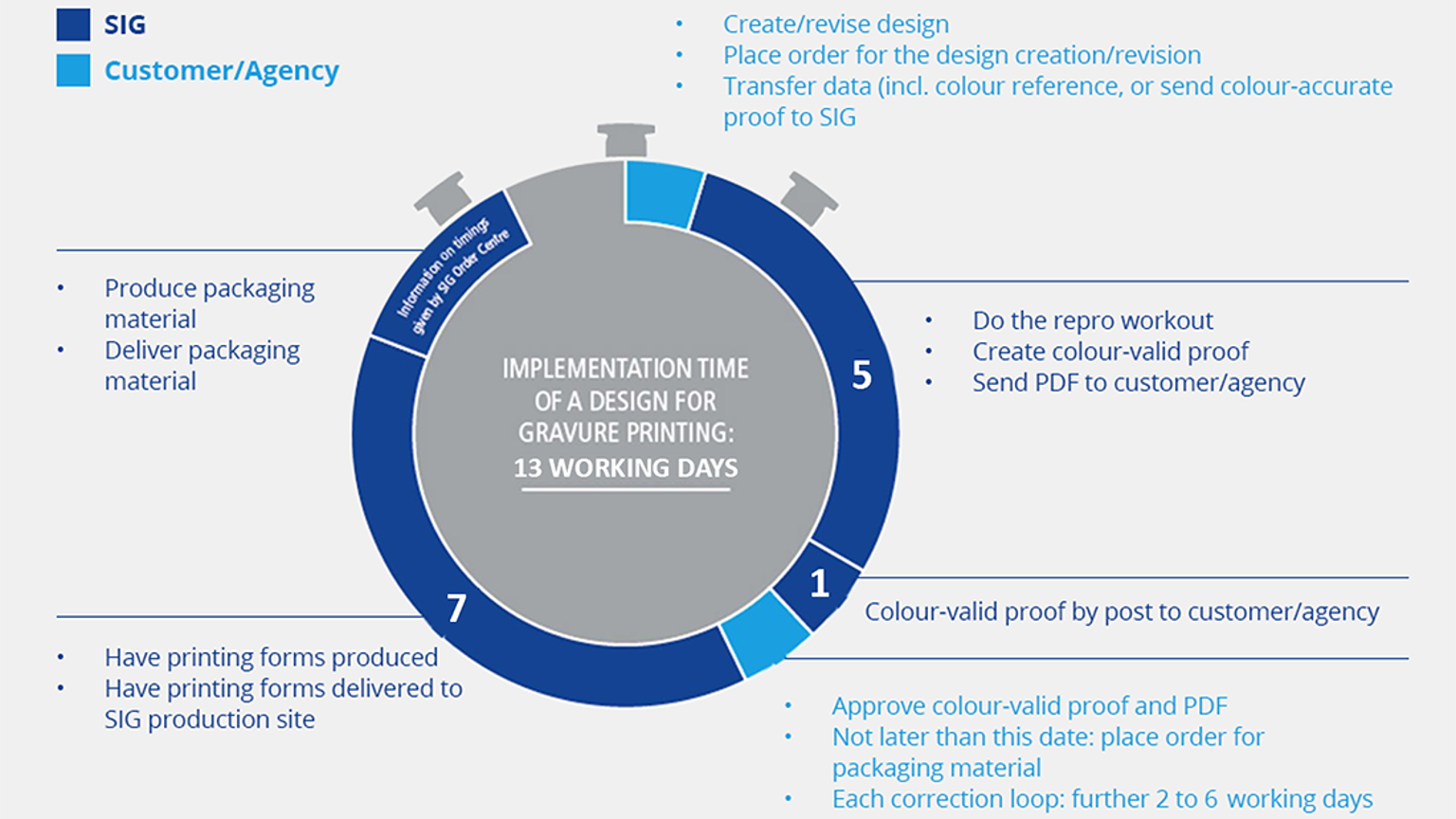
The final print journey
In the rotogravure printing process, a gravure cylinder is engraved for each print colour. All printing elements are engraved to the cylinder surface as small cells. The ink flows into each cell while surplus ink is scraped off from the print-free zones with a doctor blade. This means ink stays only in the recessed areas to be printed.
The cardboard is transferred between the gravure cylinder and the counterpressure cylinder. The ink is then transferred onto the cardboard. Our gravure printing machines have five, or in some cases six, printing units, so 5-6 different colours can be applied to the cardboard.
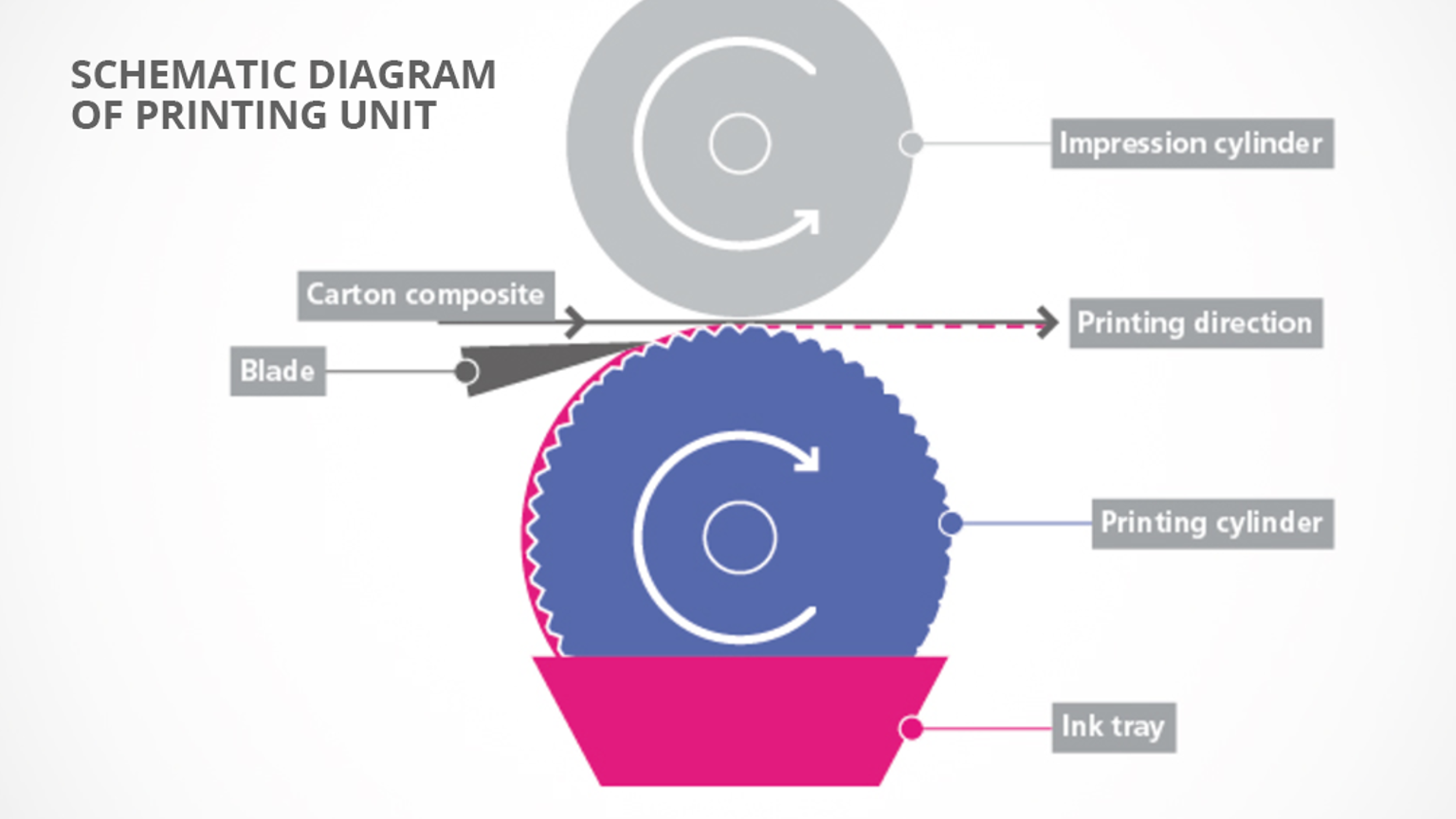
Our printing process
Schematic diagram of printing machine
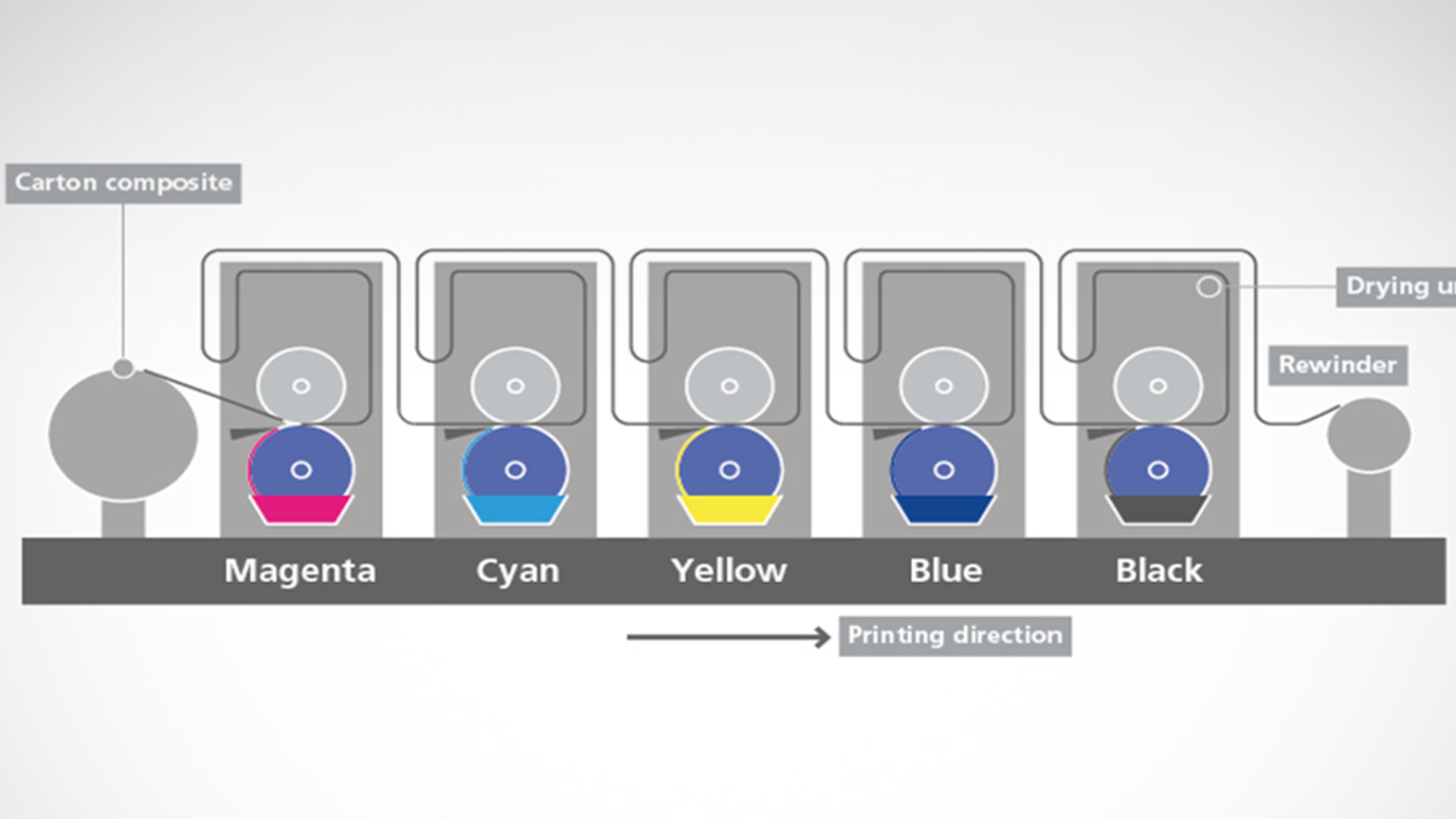